The focus of this stage is to make sure that the action item created in the Improve phase is well-implemented and maintained. Thus virtually no output is out of specification.
Control Chart Limits Ucl Lcl How To Calculate Control Limits
Formulas for Control Limits The following formulas are used to compute the Upper and Lower Control Limits for Statistical Process Control SPC charts.
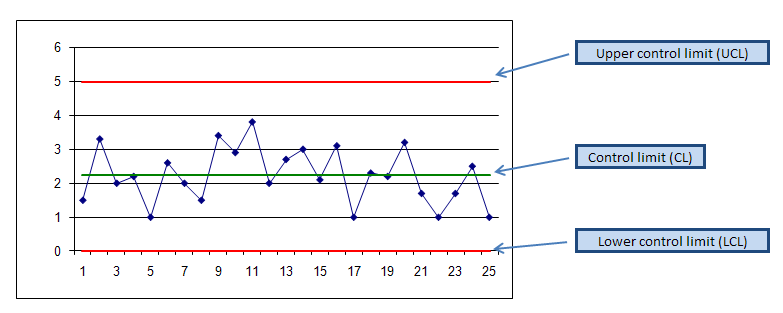
Control limits six sigma. Viewing 4 posts - 1 through 4 of 4 total. Matt did you ever come up with a solution that properly sets control limits at plus and minus 3SD from the mean automatically based on data. We can have the upper warning line and lower warning limit also.
Control limits are the limits of expected variation of either individuals data or sample subgroup data. The upper control limit and lower control limit are three standard deviation distance from the center line in both sides. If this condition is met this means that a degree of perfection of almost 100 is in place.
Specification limits are the targets set for the processproduct by customer or market performance or internal target. If you are plotting range values the control limits are given by. Six Sigma DMAIC Charts Control charts can be used for various things including determining process stability monitoring processes finding the root causes of special variations or assignable causes that go outside the expected control limits predicting a range of process outcomes and analyzing process variation patterns.
Six Sigma therefore stands for six standard deviations. Note that specification is not used in control charts because it has nothing to do with stability. Activities such as checking the.
Six Sigma iSixSigma Forums Old Forums General Control Limits This topic has 3 replies 4 voices and was last updated 18 years ago by tottow. One way that a six sigma practitioner can determine whether or not they have a smoking gun meaning that they have unexpected variation is if a point goes out of control on a control chart. Remove those subgroups from the calculations.
If the points are out of control in R chart then stop the process. So for each set of control limits there is a location parameter and a dispersion parameter. You may also like.
The location parameter simply tells us the average of the distribution. A process operating at 6 sigma means that the process average is 3 sigmas away from the closest specification limit 3 from the UCL and 3 from the LCL. Several tools are used in this stage to make sure that variables are within its limits.
Statistical Process Control Overview. Control limits are statistical process control tools which allow you to determine whether your process is stable and in control or trending towards increased variability which could lead to defects in the end product. Control charts in theory are used in product and process development to analyze processes.
Identify the special cause and address the issue. The six sigma quality system relies heavily on statistical process control or SCP and statistical analysis. Six Sigma is a philosophy and a mindset for quality improvement used by companies and organisations.
In concrete terms Six Sigma means that the companys processes maintain six standard deviations from the mean value of the process to the nearest tolerance limit. The last phase of Six Sigmas DMAIC model is the Control phase. The X bar chart control limits are derived from the R bar average range values if the values are out of control in R chart that means the X bar chart control limits are not accurate.
Use this chart to determine the Upper Control Limit UCL and Lower Control Limit LCL for a Xbar-R chart. In the control chart these tracked measurements are visually compared to decision limits calculated from probabilities of the actual process performance. Mean and Range Xbar-R chart is used when you have Continuous data with a Sample Size of less than eight.
Typically the acceptable limits of variation equates to what one would expect to see in a random process 9973 of the time. Control limits on the other hand are the indicators of the variation in the performance of the process. The one which alarms us if data points crossing this limit this can make the process unstable.
Manage Control Limits When Implementing Statistical Process Control 1554 By Rufina Scott 0 Comment. Methodology Six Sigma Control Chart Construction. Yes Control limits and Specification limits are different.
Now the question is which is the two standard deviation in distance from the central line. Control Limits for Xbar-R chart - Benchmark Six Sigma Control Limits for Xbar-R Chart Hint. DMAIC A Six Sigma Process Improvement Methodology.
In short it is the intended result on the metric that is measured. UCL AverageR 3SigmaR LCL AverageR - 3SigmaR where AverageR average of the range values and SigmaR standard deviation of the range values. Statistical process control SPC is the application of statistical methods to identify and control the special cause of variation in a process.
This is the required minimum clearance of the tolerance limit. Sigma Greek letter σ refers to the standard deviation from the mean value. The method focuses on minimising waste by minimising variations in processes.
The primary Statistical Process Control SPC tool for Six Sigma initiatives is the control chart a graphical tracking of a process input or an output over time. SPC Objectives benefits Shewhart control charts Variations Common cause variation random variation Special nonrandom variation Variables Attribute Selection of Variable Rational Subgrouping Schemes Sources of Variability. Values for A2 A3 B3 B4 D3 and D4 are all found in a table of Control Chart Constants.
Just came by this thread looking for PowerBI tools for typical DMAICSix Sigma type statistical visualizations.
That is like one wrong drug prescription in twenty-five years. We take the number of defects multiply by 1 million then divide by the total opportunities which in itself is the product of the number of units and the number of defect opportunities per unit.
Six Sigma Calculator Calculates Sigma Dpmo Dpm Yield Rty And Sample Size For Process Qualitiy Control
As the Sigma level goes to 6 you can see DPMO goes to 34 the familiar DPMO target.
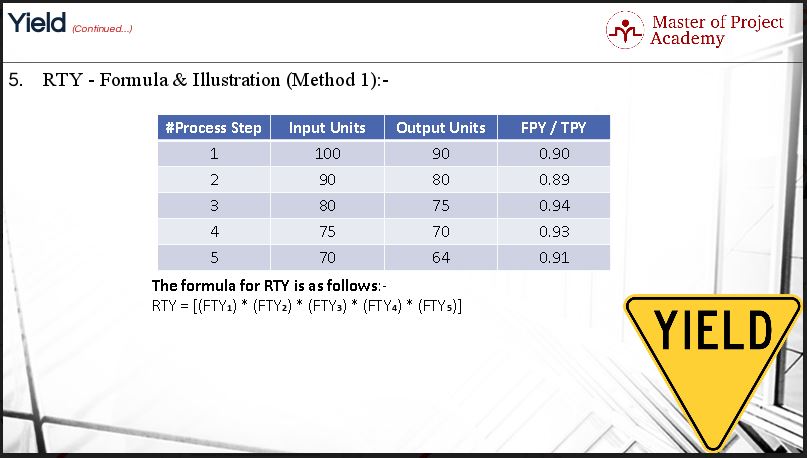
Six sigma yield calculation. Based on the Process Sigma Table Six Sigma rating should have 9999966 yield. A preferred metric is the throughput yield. The percentage of products or services without defects is the yield.
On average 85 of units will have no defects. The FTY for process A is 90100 9. Multiplying this by 1000000 gives the DPMO so at 15 sigma level thats a DPMO of 500000.
Six Sigma aims for a state in which variation appears only 34 times per every million opportunities. Assumptions No analysis would be complete without properly noting the assumptions made. Yield in Six Sigma is a classic process performance estimate.
Calculate yield by using the equation below. 2 ways to calculate Six Sigma for Continuous and Discrete data Learn Process Sigma calculation in simple easy steps without the need of using any calculator you can use Excel to do all your calculations. Code to add this calci to your website Just copy and paste the below code to your webpage where you want to display this calculator.
Each step has a yield of about 90 percent. 20 parts with critical errors in random sample of 400 parts. Calculate the yield number out of stepnumber into step of each step.
Sigma process levels 1-6 have a theoretical defect rate that is set as follows. Defects Per Unit DPU 60 defects 400 units 015 15. Like Kaizen continuous improvement Six Sigma is a state of being that one must achieve.
You can convert from a proportion such as 0986 to perhaps a more familiar percentage scale by simply multiplying the proportion by 100. A the number of units produced b the number of defect opportunities per unit. This is what we might refer to as the Six Sigma state.
100 units enter A and 90 leave. Use the process map as a guide for evaluating each individual process. Defect opportunity and defect rate.
80 units go into C and 75 leave. To go from percentage back to proportion divide the percentage by 100. You can therefore use this function to go from Six Sigma level to DPMO.
Peter a Lean Six Sigma Black Belt studied the report for a moment and then nodded. Yield 95. In this case the traditional yield is.
Throughput Yield Y t 1 DPU 1 - 015 085 85. Based on the Sigma Process Table the Six Sigma Rating is predicted to yield 9999966 percent. Organizations determine the sigma levels of given processes one sigma six sigma etc as a means of comparing the performance of those processes throughout the entire organization as distinct elements.
Let me show you whats going on he said as he picked up a marker and drew a diagram see Figure 1. To check if a BPO company is utilizing a Six Sigma process we compute for the three main components. The FTY for process B is 8090 89.
DPMO Sigma Level Yield calculation in excel for castings Foundry Lean Six Sigma. The equation for calculating defects per million opportunities is fairly straightforward. Yield is the percentage of products or services without defects.
Rework IS a part of the TPY calculation. When working on a Six Sigma project accurate methods to measure process performance metrics are critical for understanding the current state of a process and the value of changes madeFour of the most common measurements are Defects Per Unit DPU Defects per Million Opportunities DPMO Parts per Million Defective PPM and the Rolled Throughput Yield RTY. Six Sigma Calculator The calculation of a Sigma level is based on the number of defects per million opportunities DPMO.
Scrap Rate 20 400 100 5. Yield 1 DPO 100. Also called First Pass Yield Throughput Yield TPY is the number of acceptable pieces at the end of the end of a process divided by the number of starting pieces excluding scrap and rework meaning they are a part of the calculation.
To calculate FTY you would. This corresponds to a Yield the percent of units that have no defects of 95. In addition the calculations are made with using one-tail values of the normal distribution.
Example of Six Sigma Calculation A project is based on a billing mechanism. In the above table we have assumed that the standard sigma shift of 15 is appropriate the process sigma calculator allows you to specify another value the data is normally distributed and the process is stable. Online statistics calculator which calculates the DPMO defects yield and process sigma from the given values.
To calculate process yield we use the following formula. Yield Output Input 100 - Scrap Rate EX. Process Sigma is also known as Six Sigma and both the terms are same.
Instead of being satisfied with 95 success 9999966 is the ideal goal. Zooming in on the right hand side of the graph and multiplying by 1000000 gives. 90 units go into B and 80 units leave.
Process with 10 Steps This process has 10 separate steps Peter began.
ads
ads
Slide Acceptance
Search This Blog
Blog Archive
- January 2023 (11)
- September 2021 (53)
- August 2021 (47)
- March 2021 (7)
- February 2021 (23)
- January 2021 (25)
- December 2020 (66)
- November 2020 (47)
- October 2020 (8)
- September 2020 (24)
- August 2020 (31)
- July 2020 (73)
- June 2020 (71)
- May 2020 (73)
- April 2020 (73)
- March 2020 (28)
- February 2020 (17)
- January 2020 (19)
- December 2019 (44)
- November 2019 (44)
- October 2019 (44)
- September 2019 (32)
Labels
- 12th
- 13th
- 1973
- 1976
- 2007
- 2010
- 2013
- 70th
- abbreviation
- about
- abroad
- acceleration
- access
- accompaniment
- accounting
- accounts
- acid
- action
- activate
- adding
- adjust
- adjustment
- administration
- administrator
- adobe
- adrenal
- adwords
- aerator
- aero
- aerobics
- affect
- affirmations
- after
- algebra
- allied
- allowances
- altitude
- aluminum
- amendment
- amplifier
- analog
- analysis
- anatomy
- android
- angle
- angles
- angular
- animate
- anion
- annuities
- answers
- anvil
- aoss
- apostrophes
- applescript
- approach
- april
- arabic
- archaea
- archive
- area
- aristotle
- arrow
- asset
- assigning
- assistance
- associative
- asus
- atah
- atomic
- attack
- autocad
- automatic
- backup
- balance
- ball
- bang
- banging
- banjo
- baruch
- base
- basic
- basics
- basket
- basketball
- bass
- become
- beef
- beer
- beers
- beginners
- beginning
- belief
- beliefs
- best
- better
- betting
- between
- bids
- binary
- binomial
- birds
- bisect
- bisector
- blending
- block
- blood
- blur
- board
- body
- bohr
- boiler
- boker
- bonding
- bonds
- book
- bookkeeping
- bookmark
- books
- boot
- bootcamp
- borrowing
- boson
- brain
- breakdown
- breathing
- brew
- brim
- brush
- buddhism
- burns
- bush
- business
- buying
- cable
- cage
- calculate
- calculating
- calculation
- calculator
- calculators
- calculus
- california
- called
- calls
- camcorder
- camping
- canadian
- canon
- cardio
- cards
- caring
- carrots
- case
- castrate
- catalytic
- catholic
- catholicism
- cattle
- caucus
- caulk
- cavity
- ceiling
- cell
- cells
- centers
- champagne
- change
- charged
- chart
- charts
- cheat
- check
- chemical
- chemistry
- chess
- chest
- chicken
- chickens
- childrens
- chlorophyll
- chord
- chords
- christian
- chromebook
- church
- cipher
- circle
- circuit
- claim
- classes
- classify
- clean
- cleaned
- clef
- clicking
- clinical
- clogged
- clone
- clubs
- cluster
- cocktail
- coefficient
- collision
- color
- column
- columns
- commandments
- commands
- commons
- company
- components
- compounds
- compute
- computer
- computers
- concentration
- configuration
- confirmation
- congruence
- congruent
- conjugate
- connect
- connecting
- connection
- cons
- console
- constant
- construct
- contain
- contains
- contraction
- contractions
- contribution
- control
- convert
- converter
- converting
- cookies
- cooking
- coolant
- copy
- cords
- corinthian
- correlation
- cost
- court
- craft
- create
- creating
- credit
- cribbage
- crochet
- cross
- cryptograms
- curling
- currency
- current
- curtain
- curtains
- customize
- cycle
- d3100
- d3200
- d40x
- d7000
- data
- dealt
- decimal
- default
- definition
- defrag
- delete
- denominations
- denominator
- depreciation
- desktop
- deviation
- dhcp
- diagonals
- diagram
- diarrhea
- diesel
- diet
- difference
- different
- digestive
- digital
- dimmer
- direct
- disable
- disk
- distance
- distribution
- divides
- dividing
- division
- does
- doing
- dollar
- domain
- doors
- dosage
- double
- download
- draft
- drains
- draw
- drawings
- dresses
- drive
- drumming
- drywall
- dual
- dumbbells
- dummies
- during
- dvds
- each
- eating
- ebay
- ebook
- edge
- edges
- edit
- effectiveness
- elastic
- elasticity
- election
- electrolyte
- electronegativity
- electronics
- elimination
- elliott
- emails
- empty
- enchantments
- endings
- endosymbiosis
- energy
- engine
- enter
- entries
- entry
- equations
- equivalent
- esophagus
- estate
- evaluate
- even
- example
- examples
- excel
- exercises
- explain
- explained
- explaining
- explanation
- exponential
- exponents
- export
- expressions
- exterior
- external
- factorial
- factoring
- factory
- fade
- families
- fantasy
- fatigue
- fats
- faucet
- feet
- fertilize
- figure
- file
- files
- final
- finance
- financial
- find
- finding
- firewall
- fireworks
- fixing
- flash
- fleas
- flip
- flipping
- floor
- floors
- fluid
- folder
- food
- football
- forces
- form
- format
- formed
- formula
- formulas
- forward
- forwarding
- four
- fraction
- free
- freezing
- french
- frequencies
- friday
- fridge
- from
- front
- function
- functions
- fund
- furnace
- galaxy
- garageband
- garden
- gauge
- gearbox
- general
- geometry
- german
- gmail
- goal
- goat
- goddess
- goddesses
- gods
- goes
- gold
- golf
- goods
- gopro
- gopros
- gore
- grantor
- graph
- graphing
- gravity
- greek
- groups
- growth
- guide
- guitar
- hacking
- hand
- hangouts
- happens
- hard
- harden
- hardwood
- harmonics
- headers
- heart
- hearts
- heat
- hebrew
- hedge
- height
- heimlich
- hello
- hinduism
- history
- hockey
- holiday
- holographic
- holy
- home
- horse
- hotel
- how to
- hudson
- human
- hunger
- hyperlink
- hypotenuse
- identify
- idiomatic
- illustrator
- image
- imaginary
- immediate
- important
- indent
- inductance
- inelastic
- inertia
- inguinal
- insects
- insert
- inserting
- install
- integrals
- intermolecular
- internet
- interpret
- intervals
- inverse
- inverting
- investing
- iodine
- ionic
- iphone
- ipod
- iron
- italian
- itunes
- jason
- java
- jesus
- joints
- journal
- kamehameha
- keyboard
- kids
- kindle
- kinds
- kinematics
- kinetic
- king
- kitchen
- knit
- knitting
- lacrosse
- langstroth
- laptop
- latent
- laundry
- layer
- leaking
- leaky
- learn
- ledger
- left
- lend
- length
- letter
- letterhead
- level
- lewis
- license
- life
- light
- likelihood
- limiting
- limits
- line
- linear
- lines
- lion
- list
- listen
- living
- loans
- located
- location
- lock
- logic
- logical
- macbook
- macro
- macromolecules
- magnuson
- main
- maintenance
- major
- make
- making
- management
- managerial
- maneuver
- manufacturing
- many
- margin
- marine
- mark
- marketable
- mary
- masons
- math
- mavericks
- maximizing
- maximum
- mean
- measure
- measurement
- media
- medicare
- melodic
- membrane
- memo
- merge
- metabolism
- metal
- metalloid
- metals
- methods
- midpoint
- milk
- minecraft
- mining
- minutes
- missouri
- mite
- mixture
- mock
- model
- moles
- moment
- monitors
- mortgage
- mortgages
- mosaic
- moss
- move
- movements
- movie
- mulch
- multiple
- multiplying
- muscle
- muscles
- music
- mythology
- nail
- names
- natural
- navy
- neck
- needed
- nerve
- niels
- nikon
- noble
- noise
- nominal
- nonelectrolyte
- nonmetal
- nonmetals
- nonpolar
- nook
- notes
- nucleic
- number
- numbering
- nutshell
- obligation
- odds
- olives
- open
- operators
- options
- orbital
- orchids
- order
- organs
- osmosis
- other
- ottawa
- outlook
- output
- overeating
- overhead
- page
- pane
- paperwhite
- parallel
- parallelogram
- parliamentary
- part
- particles
- passover
- password
- paste
- pasteurize
- patriot
- pattern
- patterns
- payable
- payment
- payroll
- pearson
- pentagon
- pentatonic
- percent
- percentile
- performance
- periodic
- perpendicular
- personal
- pets
- pharmacy
- phase
- phases
- philosophy
- phone
- photoshop
- phrases
- piano
- pictures
- pipe
- pipes
- pitch
- pivot
- planning
- plans
- plants
- plasma
- plate
- plato
- players
- playstation
- pleural
- plot
- plumbing
- plus
- point
- poisonous
- polar
- polygon
- polynomials
- pool
- pops
- position
- potential
- power
- powers
- precalculus
- predecessor
- pregnenolone
- prepare
- preposition
- press
- prevent
- price
- primary
- printables
- procedure
- procedures
- processors
- products
- program
- programming
- project
- projectile
- properties
- property
- pros
- protune
- proving
- pure
- purification
- purpose
- quadrilateral
- qualification
- question
- questions
- quick
- quizzes
- quotations
- quotes
- racing
- radio
- rank
- rate
- rates
- ratio
- reactant
- reaction
- read
- real
- rebel
- receivable
- recommendation
- recommendations
- recorder
- recover
- recovery
- rectangle
- rectangles
- redstone
- reference
- reflex
- refracting
- refund
- region
- regression
- regular
- reinstall
- relating
- relativity
- remote
- remove
- repair
- repartition
- repeater
- replace
- repolarization
- rescind
- research
- reset
- residual
- restart
- resting
- restore
- resume
- retake
- reverse
- reviewing
- revision
- rhombus
- rhombuses
- ride
- river
- roberts
- roku
- roman
- rotate
- ruby
- rudiments
- rule
- rules
- running
- sage
- sales
- same
- samsung
- saturday
- saving
- scale
- scales
- scenario
- schedule
- scientology
- score
- scratch
- scratched
- scratches
- screen
- script
- scripture
- security
- seedlings
- seeds
- seek
- segment
- selection
- sell
- selling
- send
- sense
- sentences
- serve
- setting
- settings
- setup
- shade
- sharepoint
- shares
- sheet
- short
- shortcut
- shortcuts
- showing
- shuffle
- side
- sides
- sigma
- signs
- sine
- singing
- single
- sins
- siri
- sites
- skirt
- skype
- slice
- slide
- slides
- slope
- small
- smelt
- snake
- snap
- snipe
- social
- socrates
- soften
- solar
- solo
- solve
- song
- songs
- sonnet
- source
- spades
- spanish
- spark
- sparkling
- speculation
- spell
- spelling
- spotify
- spring
- stained
- stamp
- stand
- standard
- stands
- start
- starting
- statement
- statistics
- stave
- stem
- step
- steps
- stickies
- sticky
- stitch
- stock
- stocks
- storage
- stories
- story
- strap
- strategy
- string
- strings
- studio
- subatomic
- substance
- substances
- subtraction
- summary
- surface
- switch
- symphony
- symptoms
- sync
- system
- table
- tableau
- tablespoon
- tablet
- tactic
- talk
- tangent
- tank
- tanks
- team
- teams
- telescopes
- television
- template
- tennis
- terminology
- terms
- test
- testament
- tester
- tether
- tethering
- text
- theorem
- theory
- theta
- thieves
- thigh
- through
- thursday
- times
- toilet
- tool
- toolbar
- tools
- total
- trading
- tragedy
- transfer
- transistor
- transplant
- trapezoid
- trash
- travel
- treat
- treble
- triangle
- tricare
- trig
- troubleshoot
- truck
- truss
- trust
- tutorial
- tween
- type
- types
- ukulele
- understanding
- uninstall
- unit
- units
- unsaturation
- useful
- uses
- using
- utility
- value
- valve
- vaporization
- variable
- variables
- variance
- vegans
- vegetable
- vegetarian
- velocity
- vendor
- venmo
- vent
- venting
- vents
- verb
- verbs
- vocal
- voice
- voicemail
- voltage
- wade
- waist
- wake
- walking
- water
- watergate
- waterproof
- wave
- weave
- websites
- wedding
- weight
- what
- when
- where
- which
- whisker
- white
- wifi
- window
- windows
- wine
- wines
- winter
- winterize
- wireless
- wisdom
- with
- wood
- word
- work
- works
- wrap
- write
- writing
- xbmc
- yard
- yardage
- yield
- your
About Me
quizzes for kids age 5
Quiz for 5 year olds Quizzy Kid . Quizzes by age. Quiz for 5 year olds. Quiz for 5 year olds Quiz for 5...
